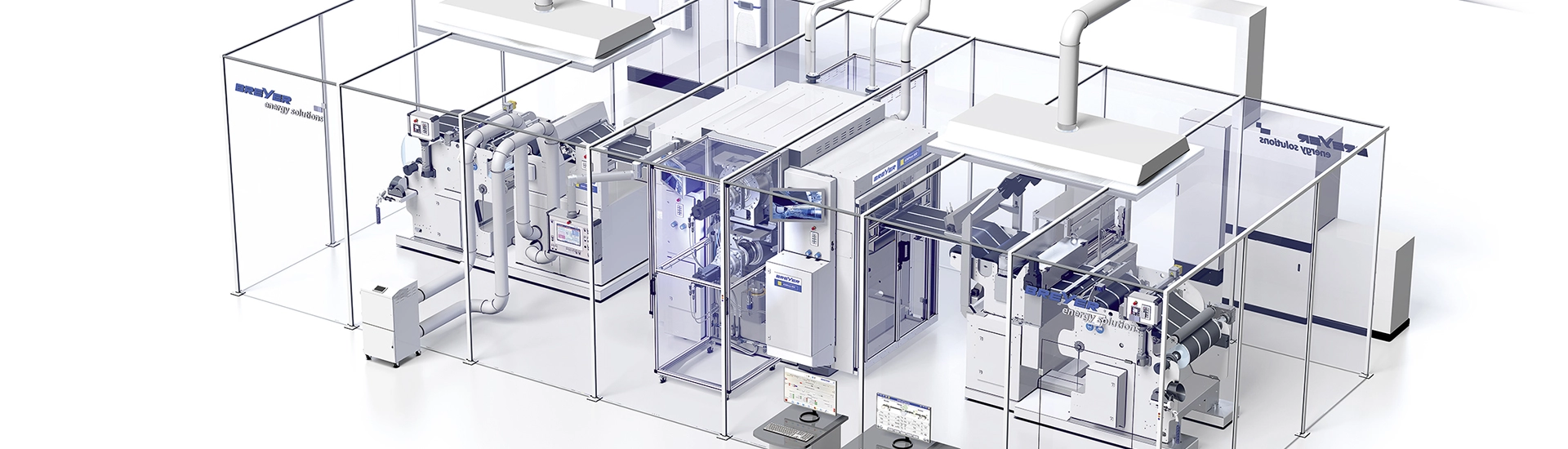
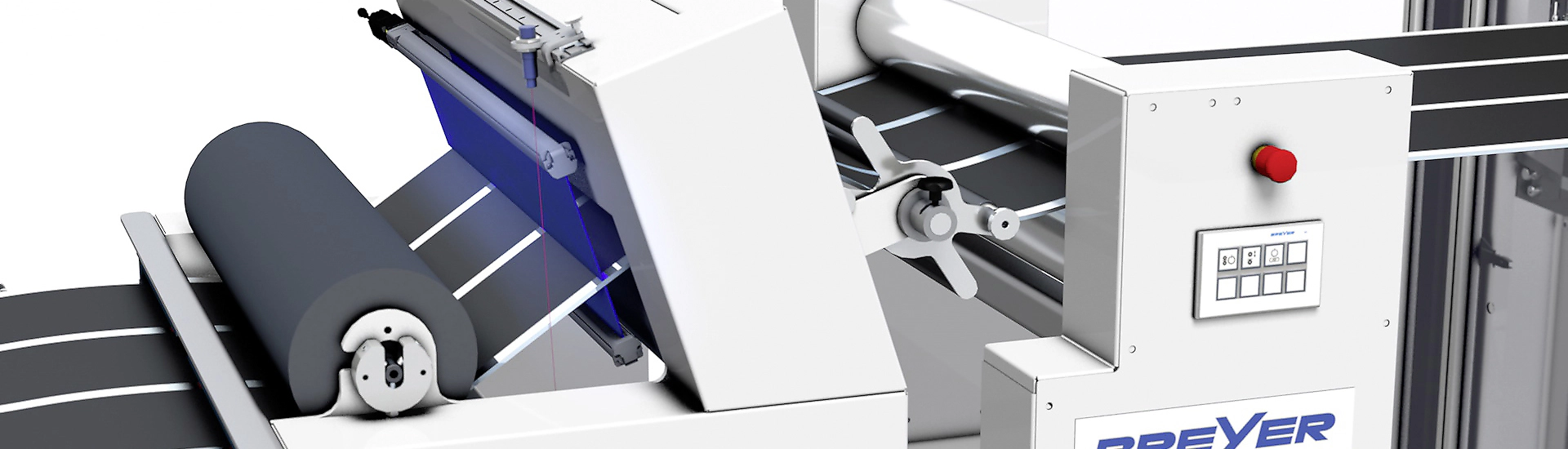

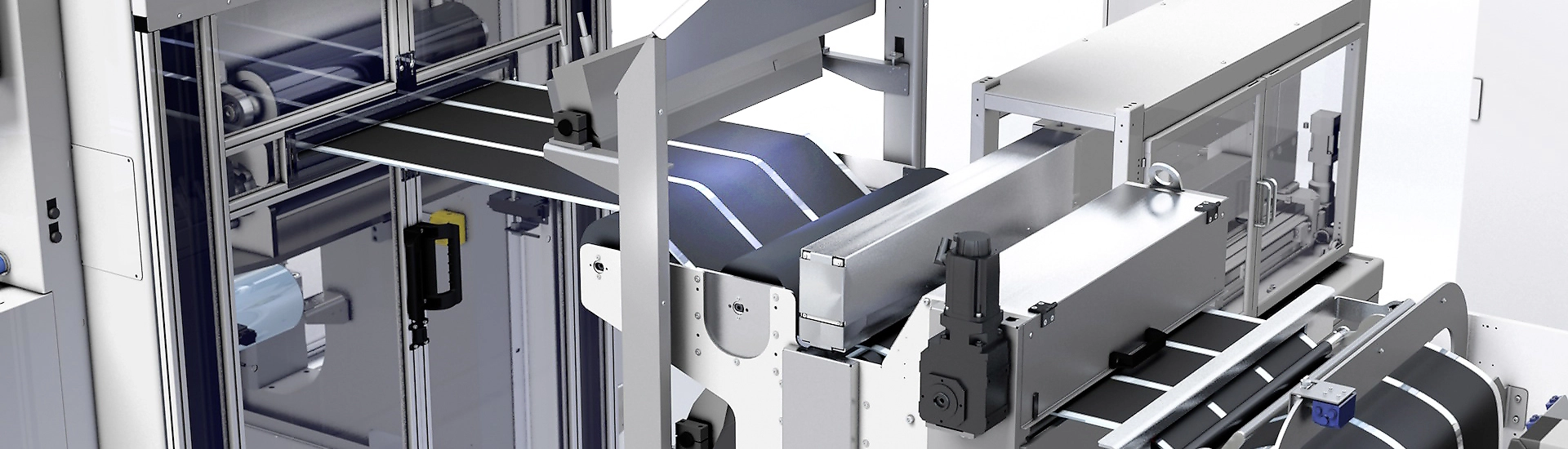
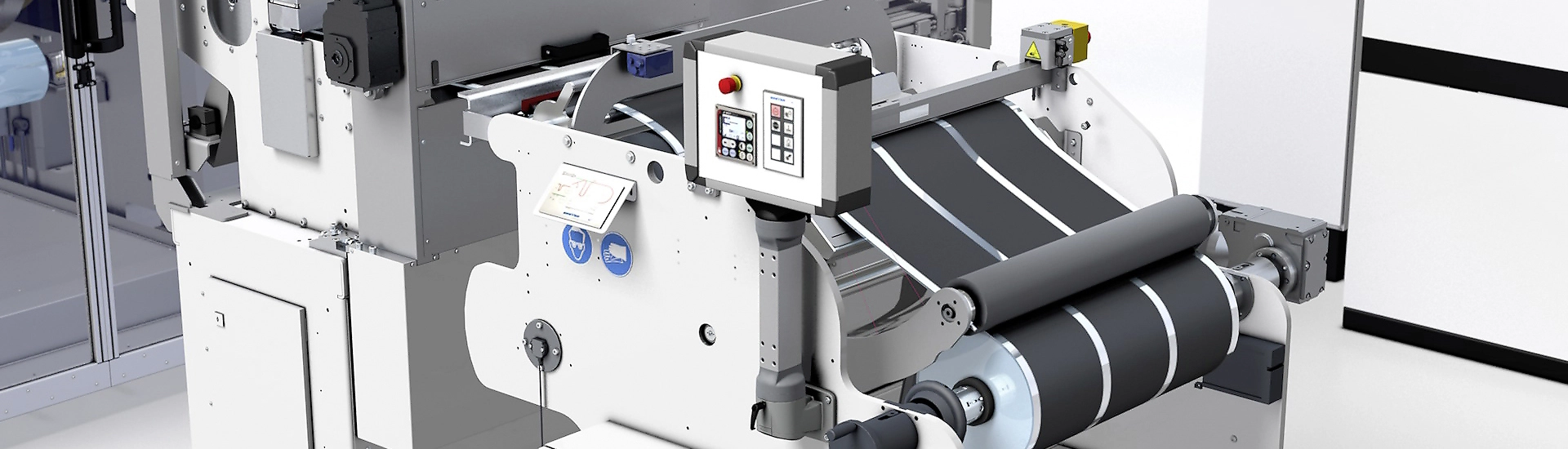
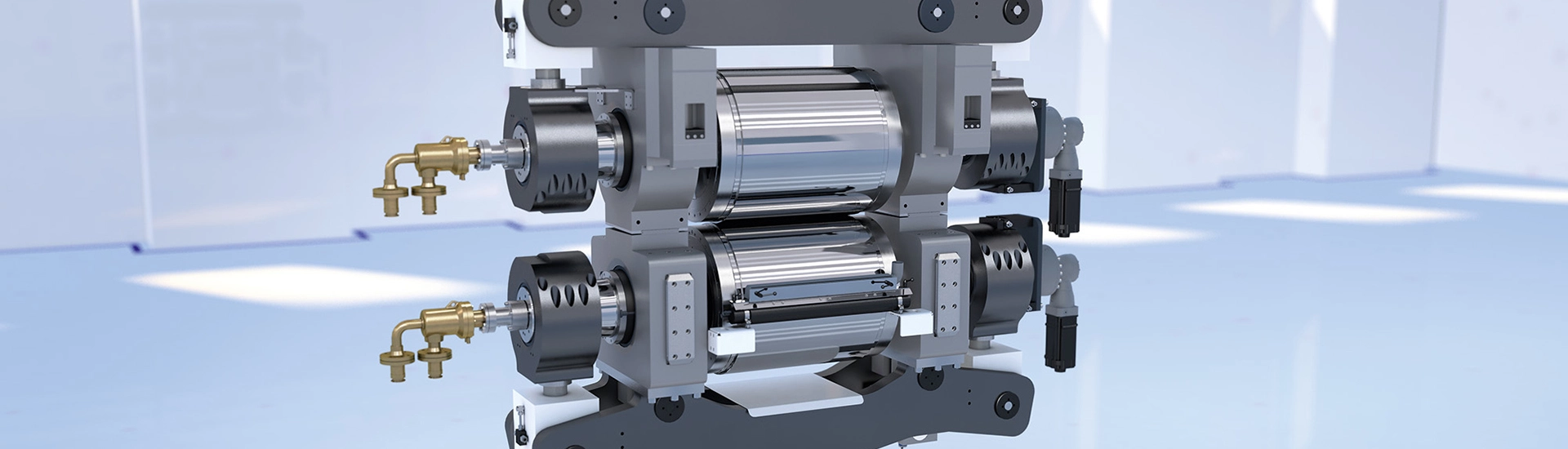
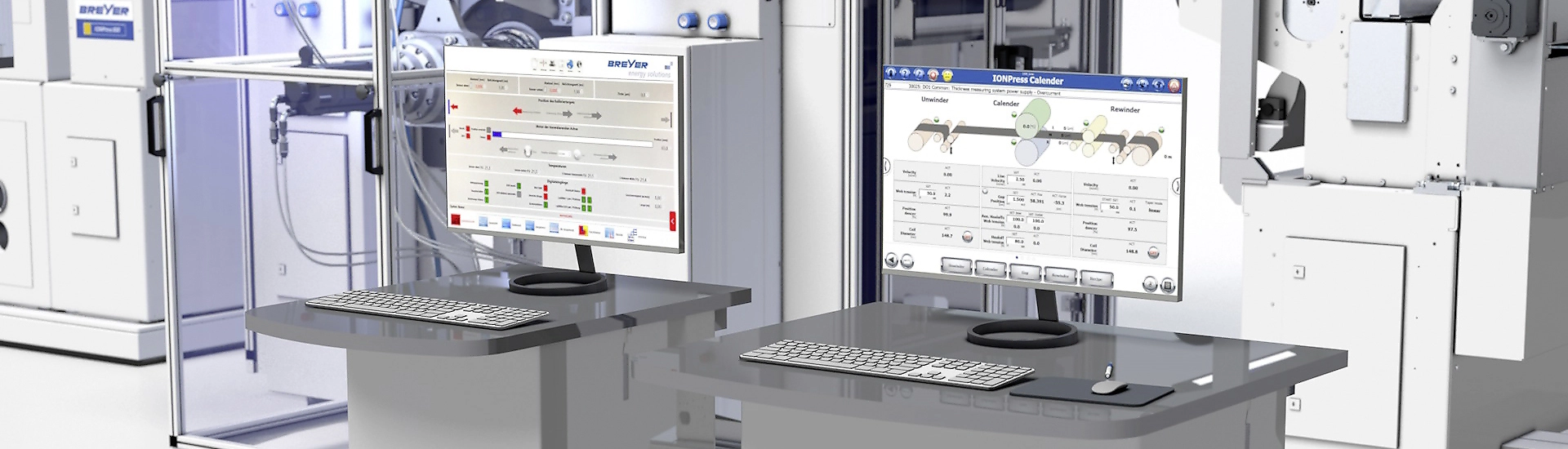
BREYER IONPress
Calander technology
Sophisticated production of electrode foils for lithium-ion batteries
The new generation of the BREYER IONPress calender represents a milestone in the improvement of lithium-ion electrode foil production.
Calander system for lithium-ion electrode production
During the calendering process, required properties such as the increase of the power density, optimized electron transport and improved contact between the particles have to be achieved.
BREYER's decades of experience in the field of calender manufacturing made it possible to develop a system that meets the high precision requirements in electrode manufacture. The precise and reliable calender system allows extremely low thickness tolerances.
It is crucial for the operator to be able to set the film thickness reliably, quickly and reproducibly. With the BREYER "fast & easy" gap adjustment technology, adjustment is almost child's play, even in these small dimensions. In connection with the inline thickness measurement, this system allows the construction of an automatic gap control.
The BREYER technology comprises the calendering of the electrode film in the “roll-to-roll” method. The complete line also includes the unwinding of the coated substrate, the inline thickness measurement, surface cleaning and the winding of the electrode film. Upon request, other system components can be integrated.
The machine is equipped with a color touchscreen and process monitoring system for convenient operation.
ADVANTAGES
- Fast and reproducible thickness adjustment
- Infinitely adjustable line load up to 4000 N/mm
- Direct gap measurement (closed loop)
- High precision compression through servo-hydraulic gap adjustment for distance and force
- Smallest thickness tolerances
- Powerful individual drives
- security system
- Compact design
- Fast Roll exchange (< 3h)
- Counter Bending system (option)
- Convenient user interface, simple operation
SCOPE OF SUPPLY
- Unwinder for manual coil changes up to 50 m/min, with tension control and web edge control.
- Automatic turret winders for highly automated systems up to 100 m/min
- Non-contact web cleaning
- Inspection systems
- Calender IONPress with 400mm, 600mm or 800mm roll width.
- NEW: Calender IONPress 400 core (laboratory)
- Roller quick exchange system (<3h)
- Optional counterbending device
- Roller cleaning
- Substrate pre-warming
- Thickness measurement systems
- Track&Trace
- Tension separation via controled haul-off's
- Winder for manual coil change up to 50 m/min, with tension control and web edge control.
- Automatic turret winders for highly automated systems up to 100 m/min
BREYER · Innovations for better Solutions
Contact us and ask about BREYER IONPress.
The future has begun - with BREYER energy solutions you will also be at the forefront.
Technical data
Line speed | 0.5 – 100 m/min |
Roller temperature control | water / thermal oil |
Roller widths | 400, 600, 800 mm |
Roller diameter | up to 800 mm |
Roller surface | hard chrome-plated / carbide |
Roller gap adjustment | servo-hydraulic control |
Precision | ± 2 µm |
Line loads | up to 4000 N/mm |
Examples of application
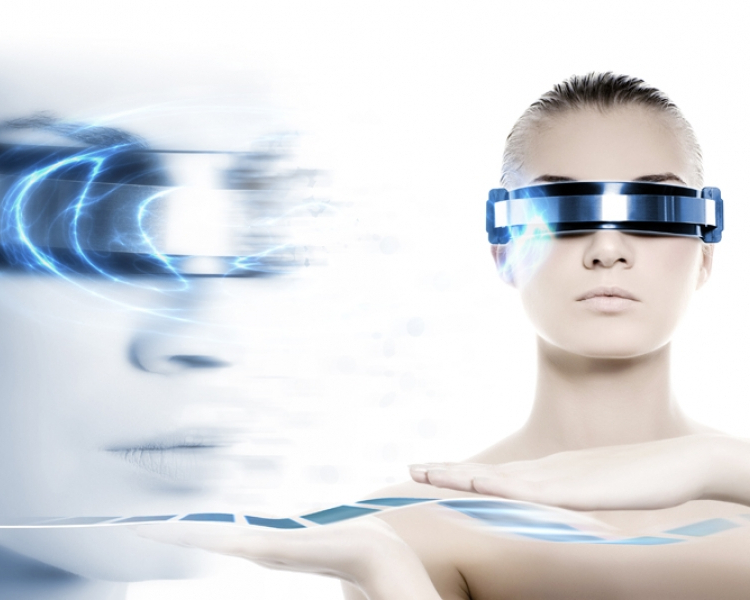
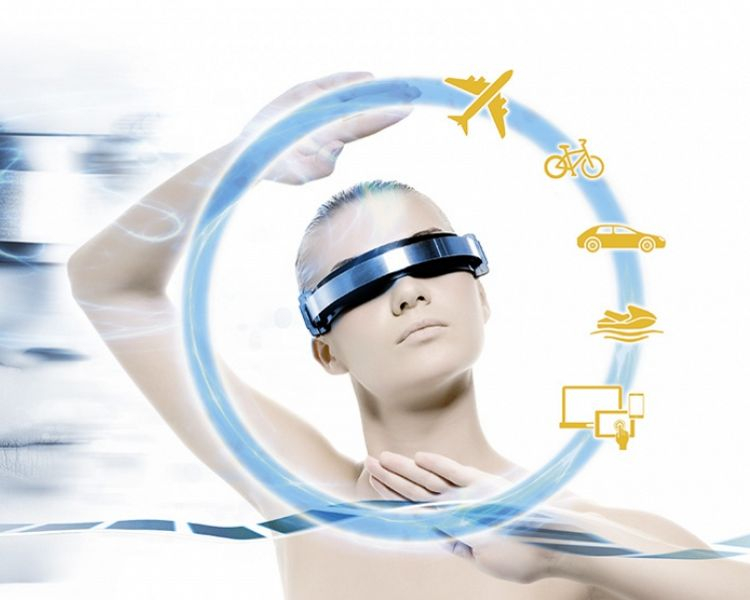
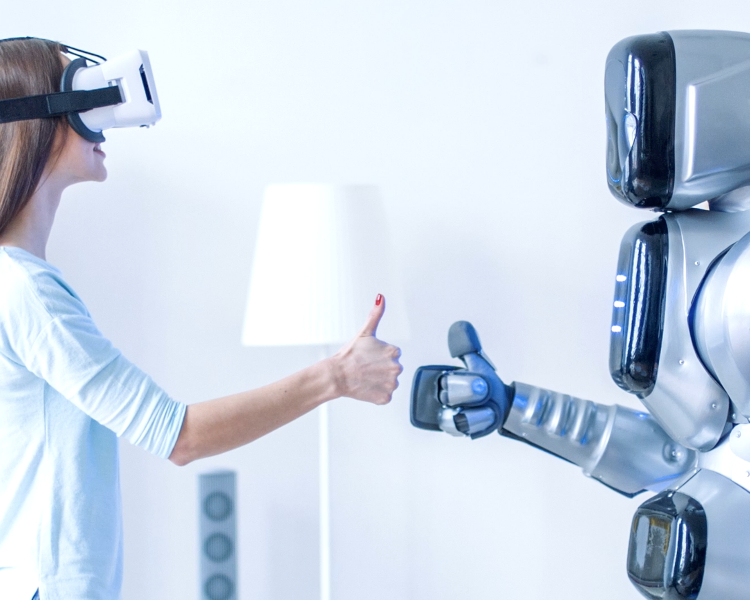
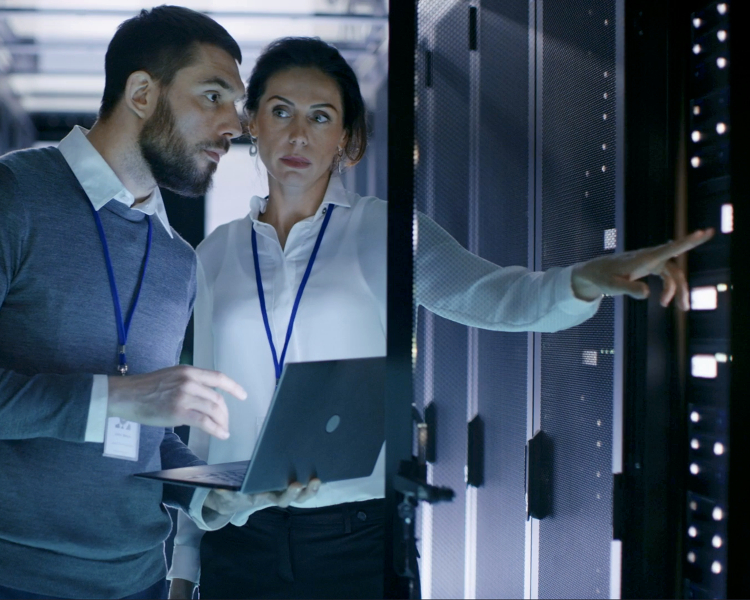
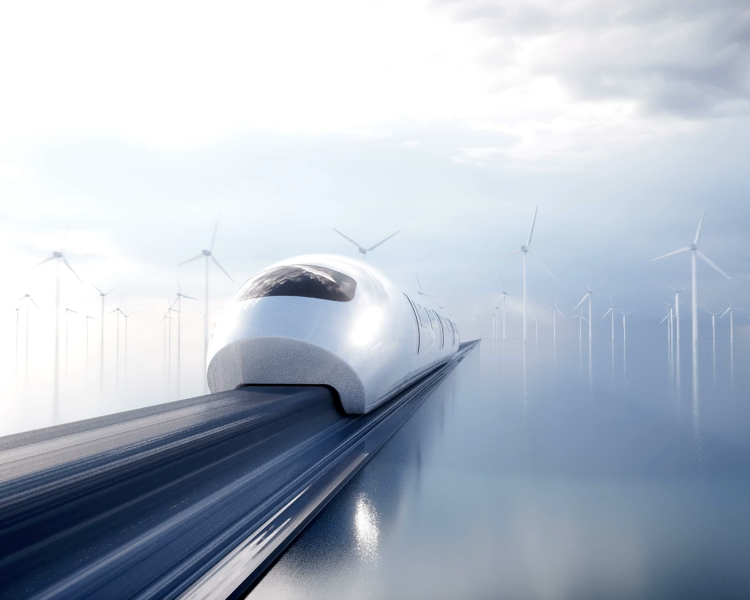
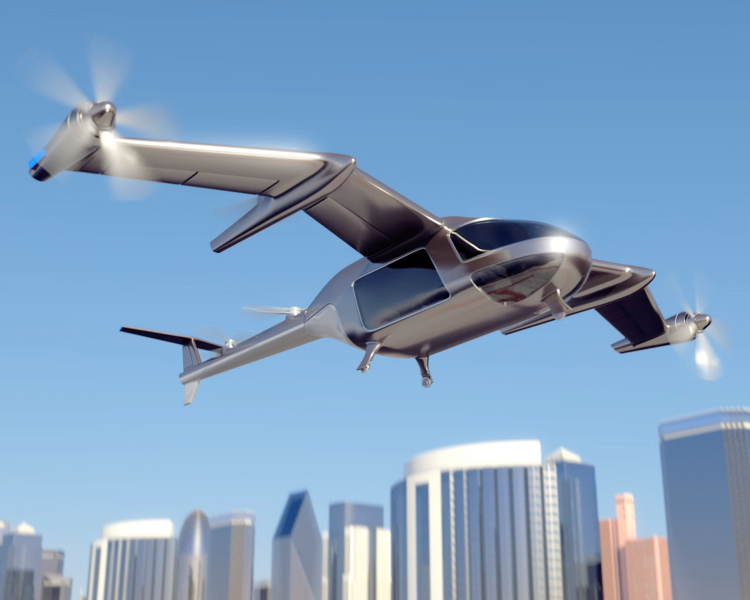
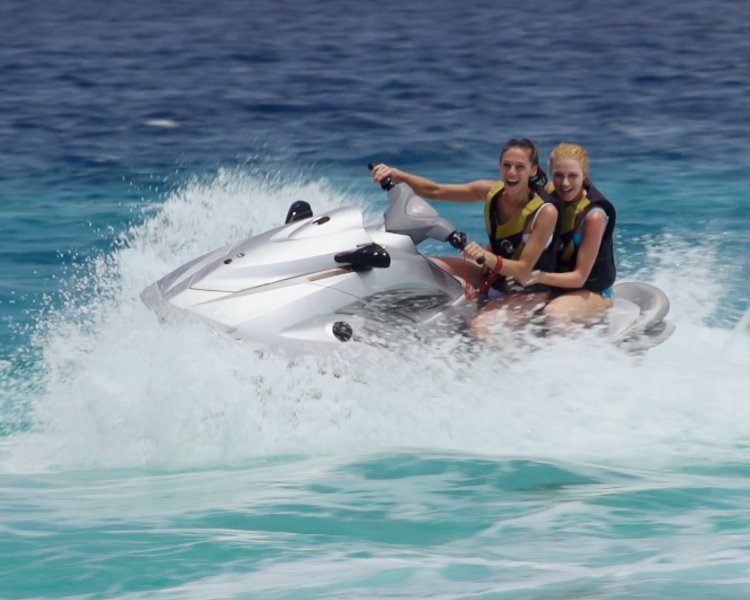
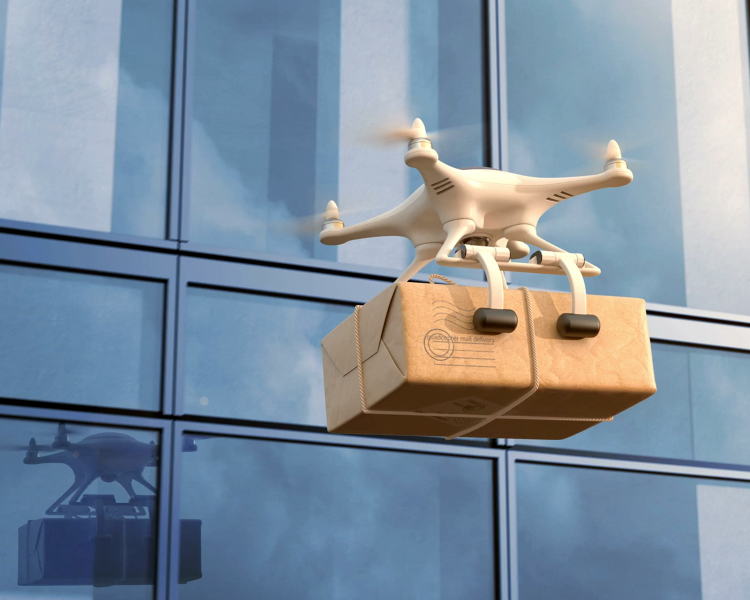
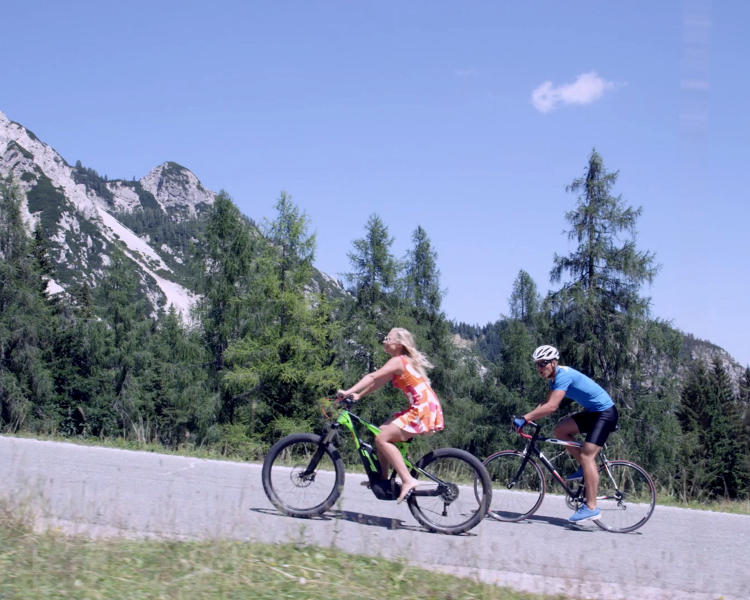
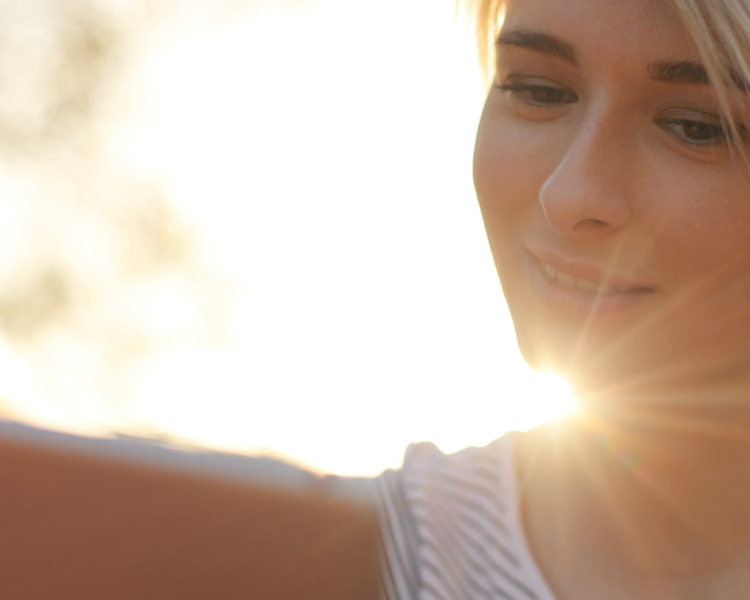
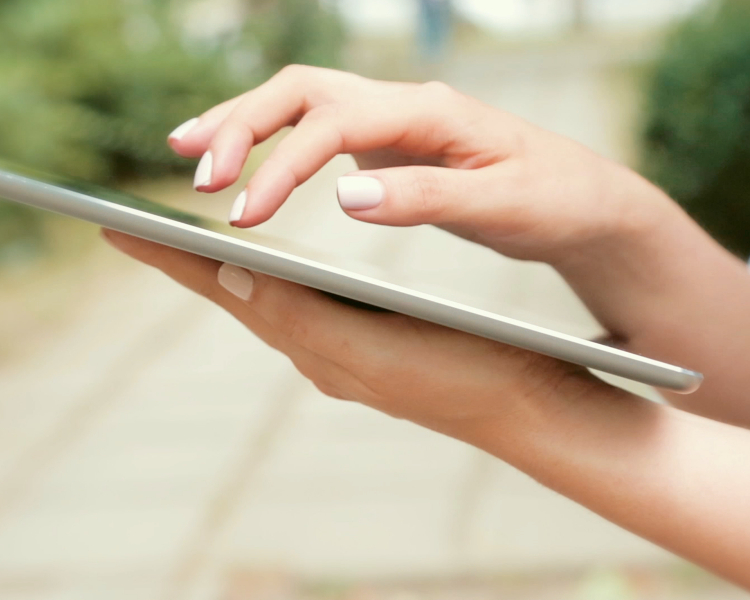
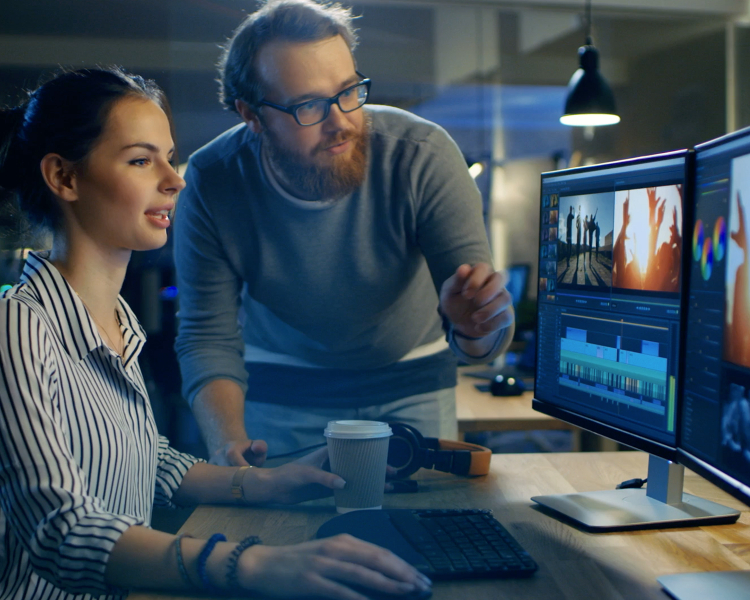
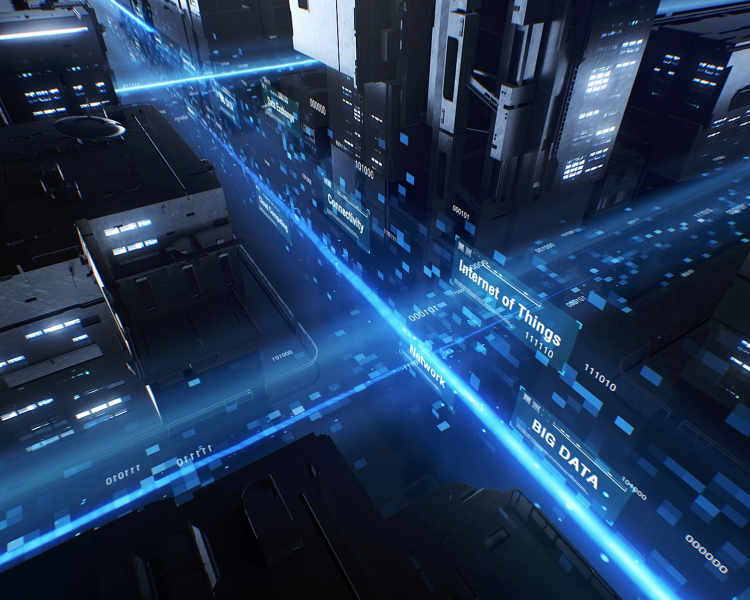
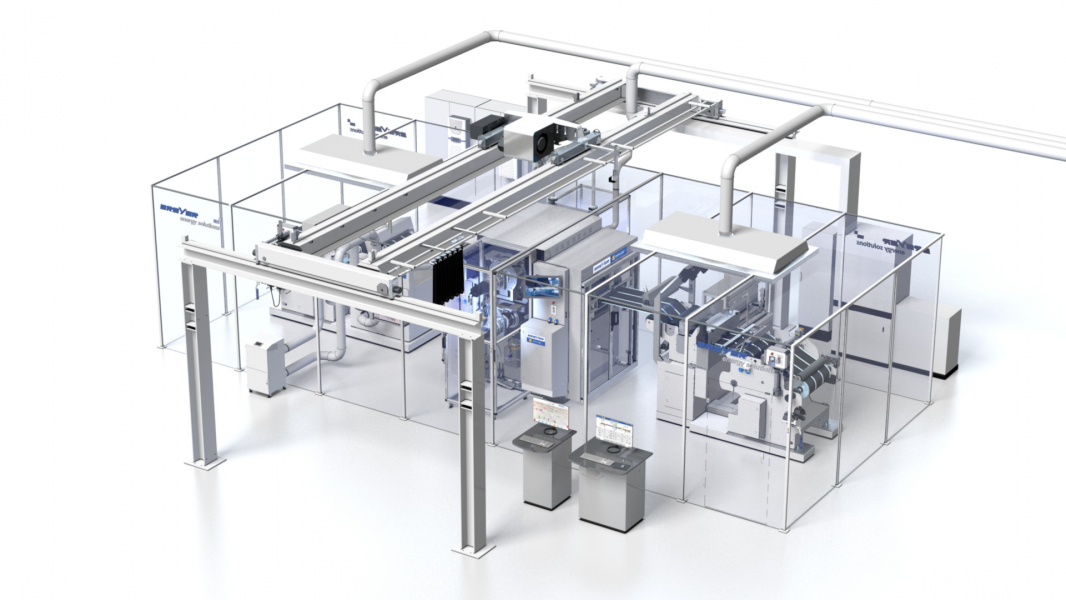
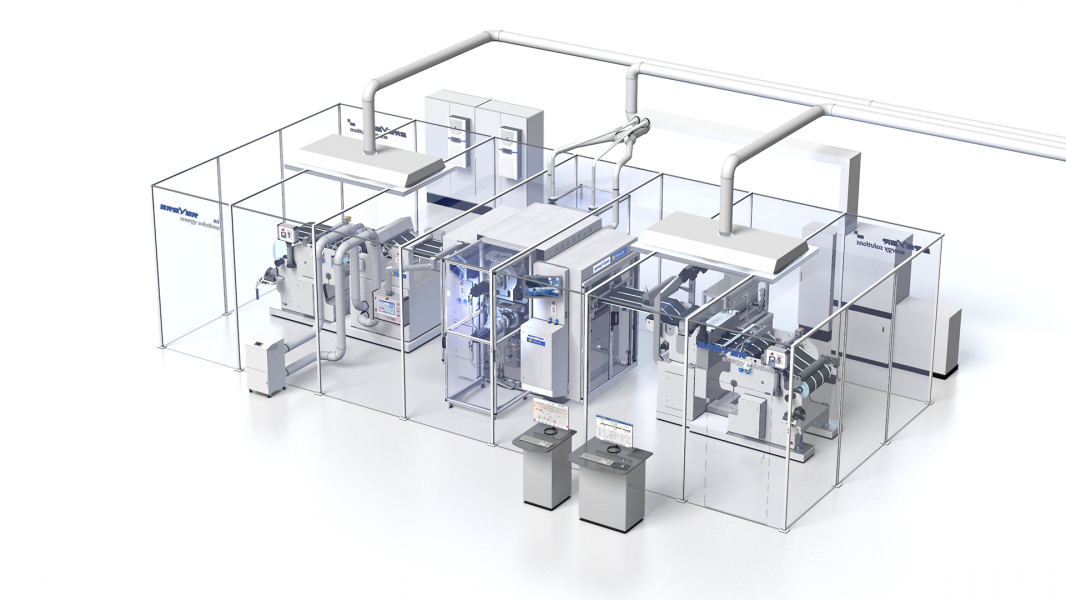
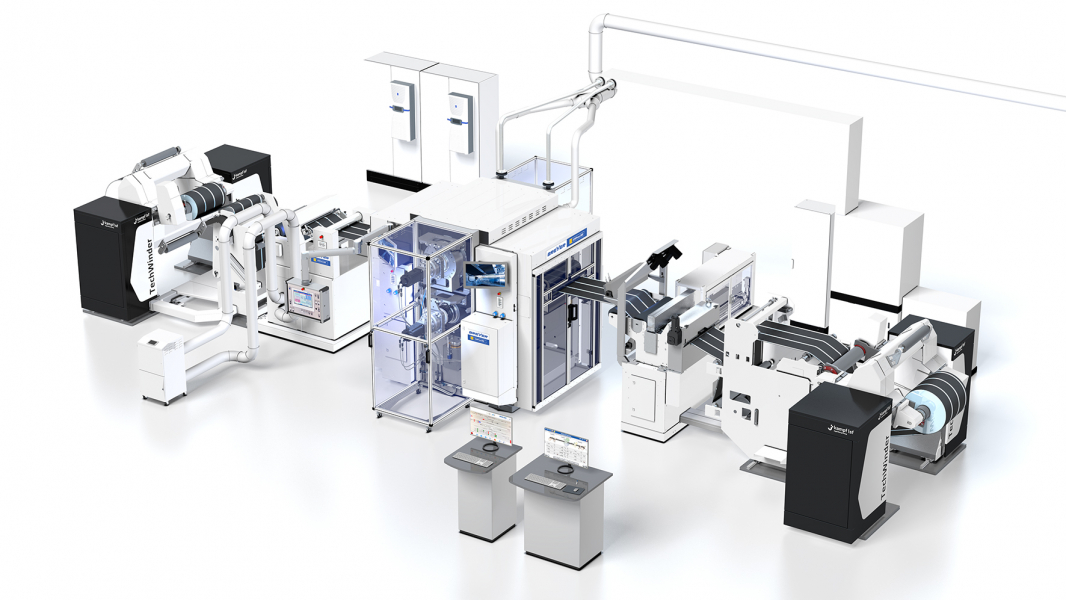
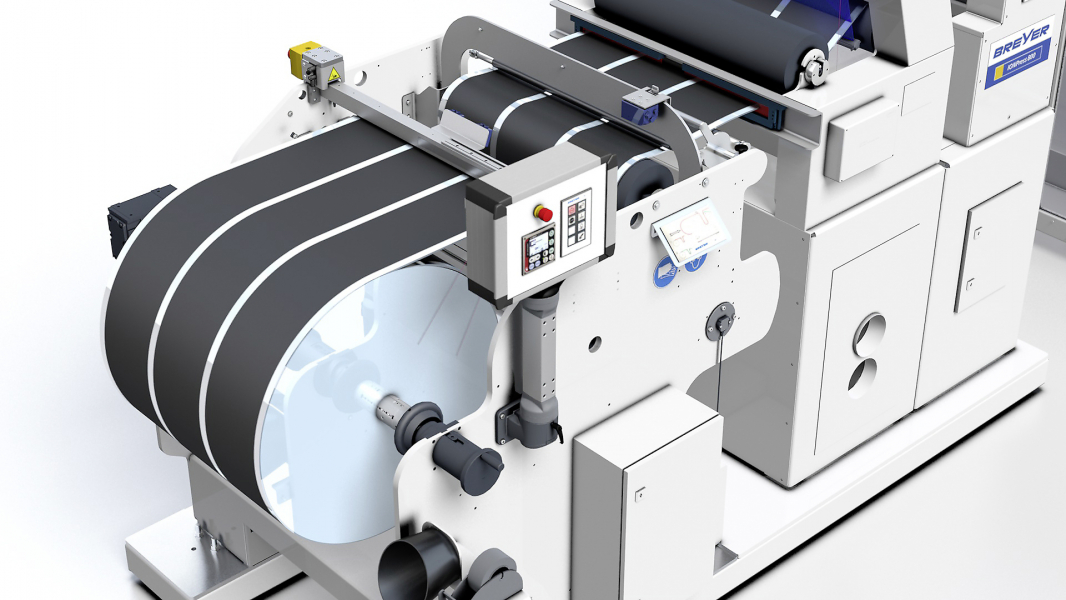
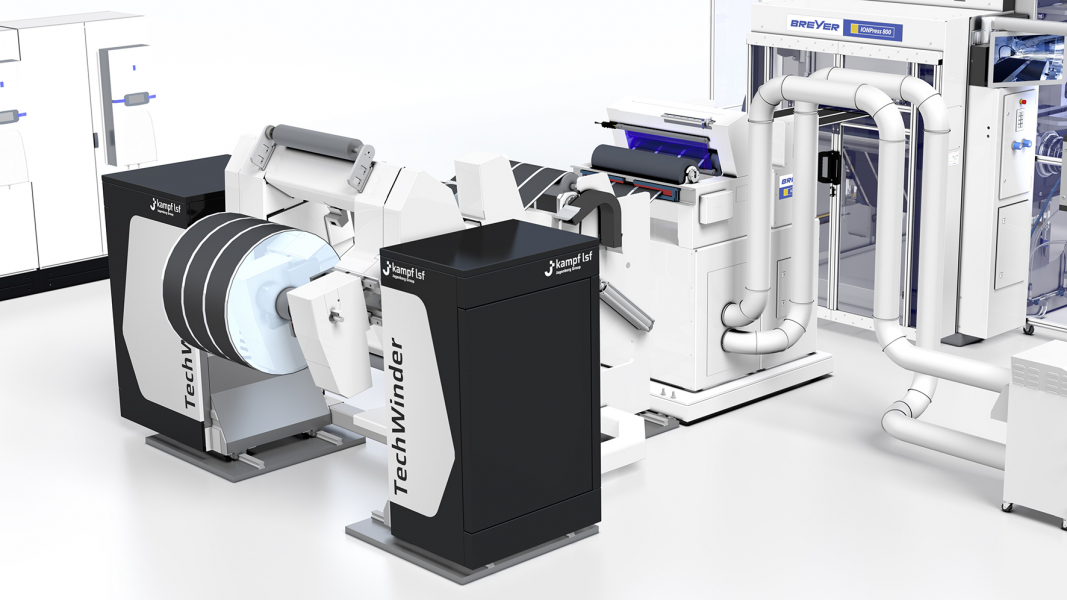
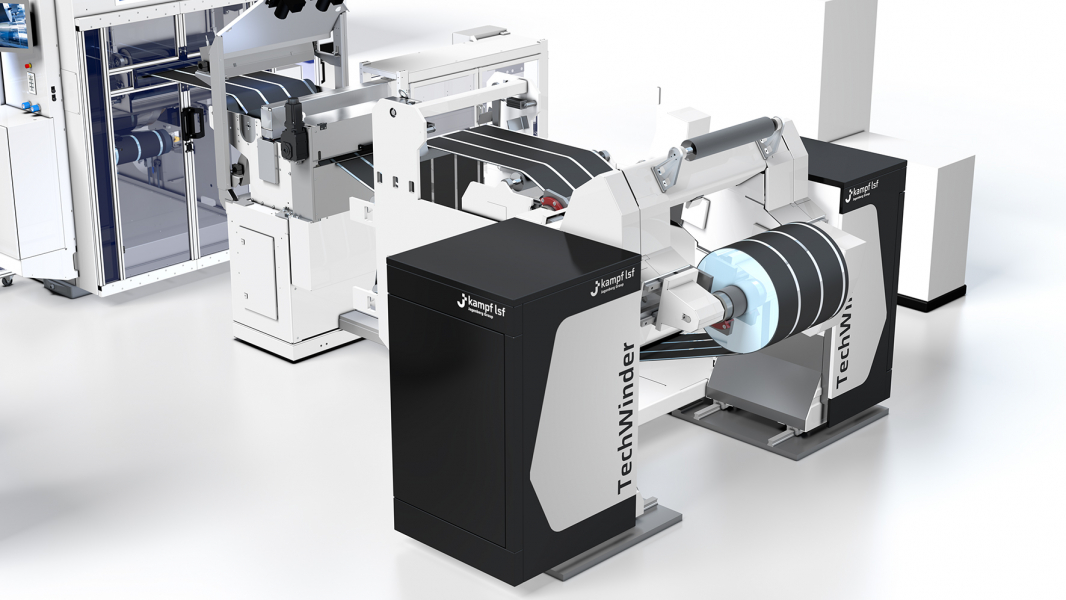
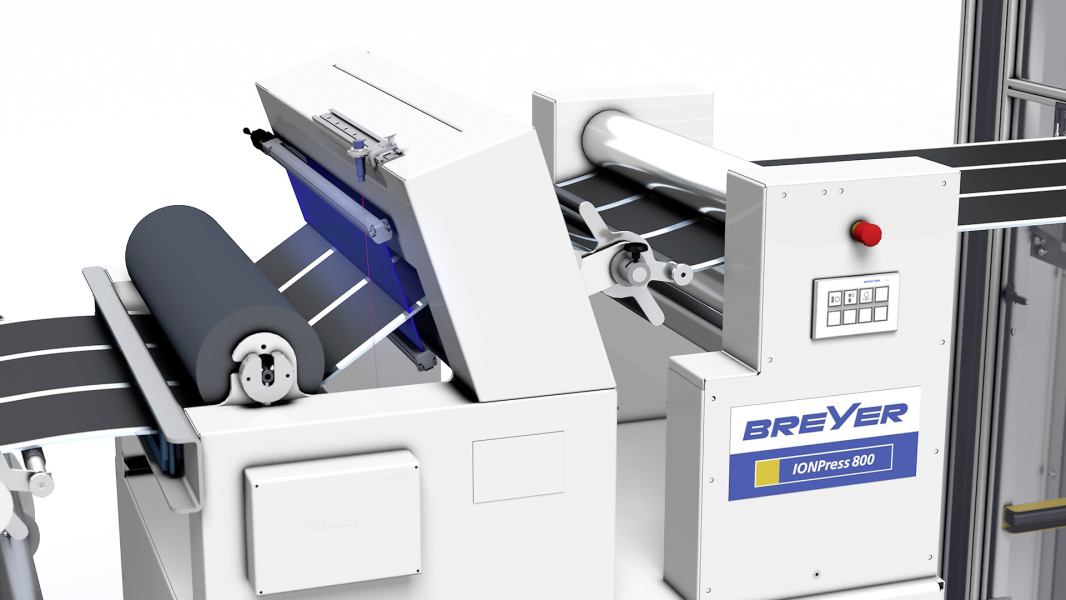
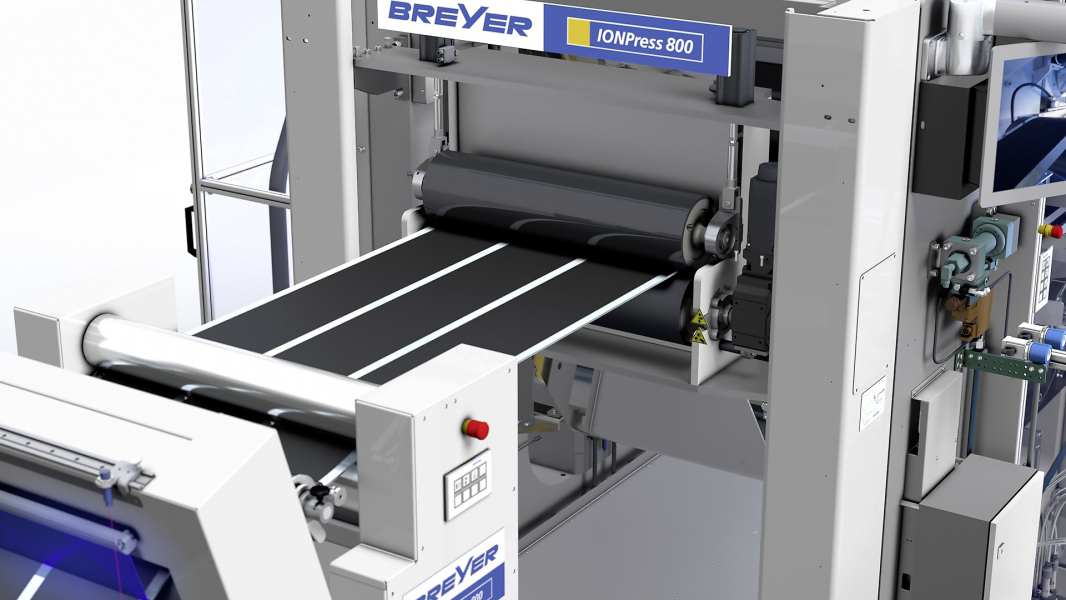
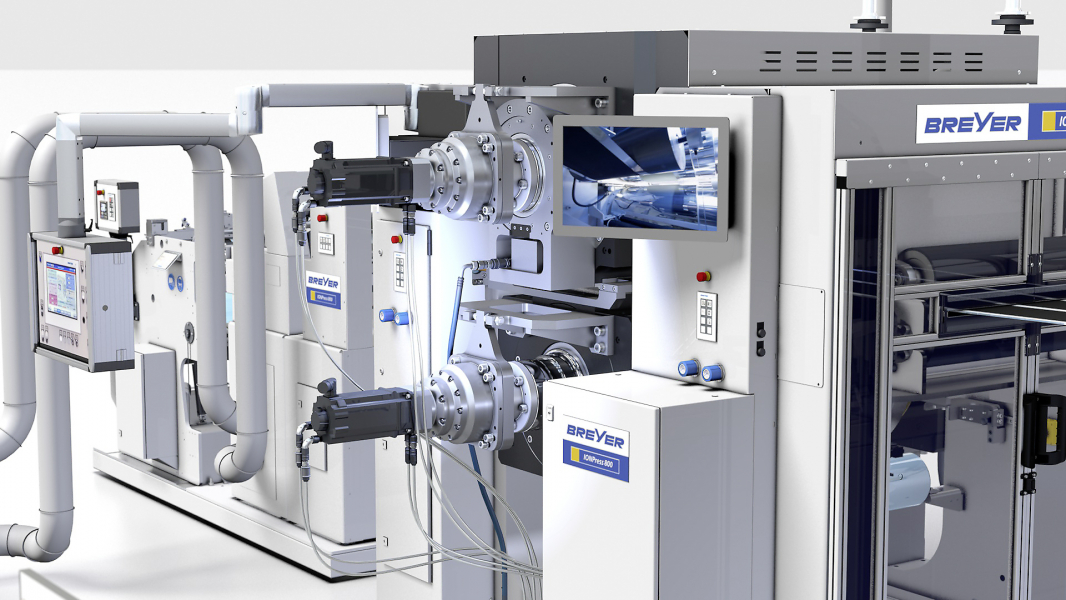
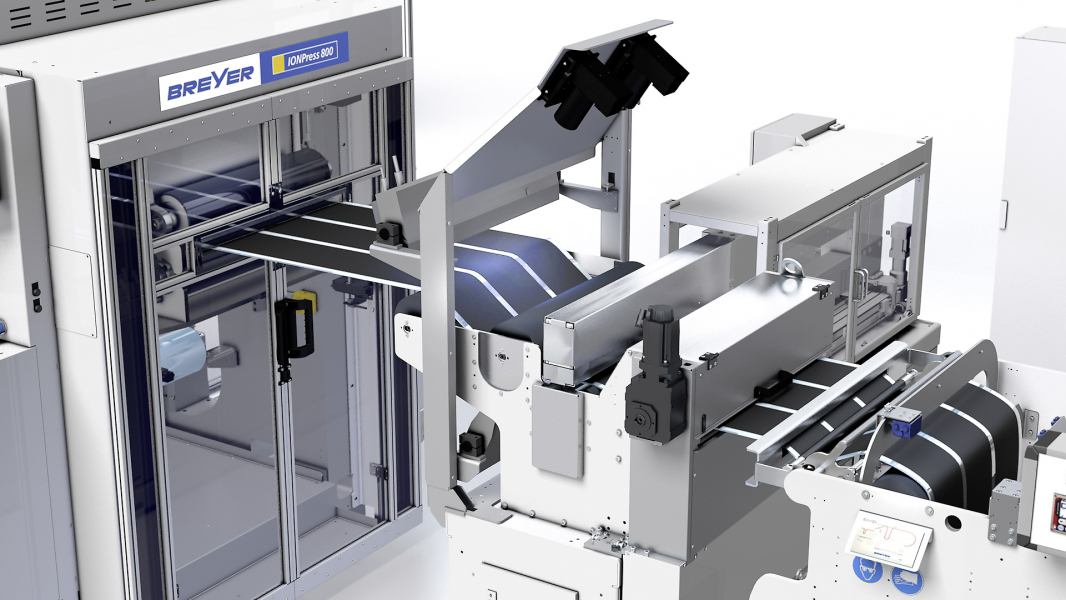
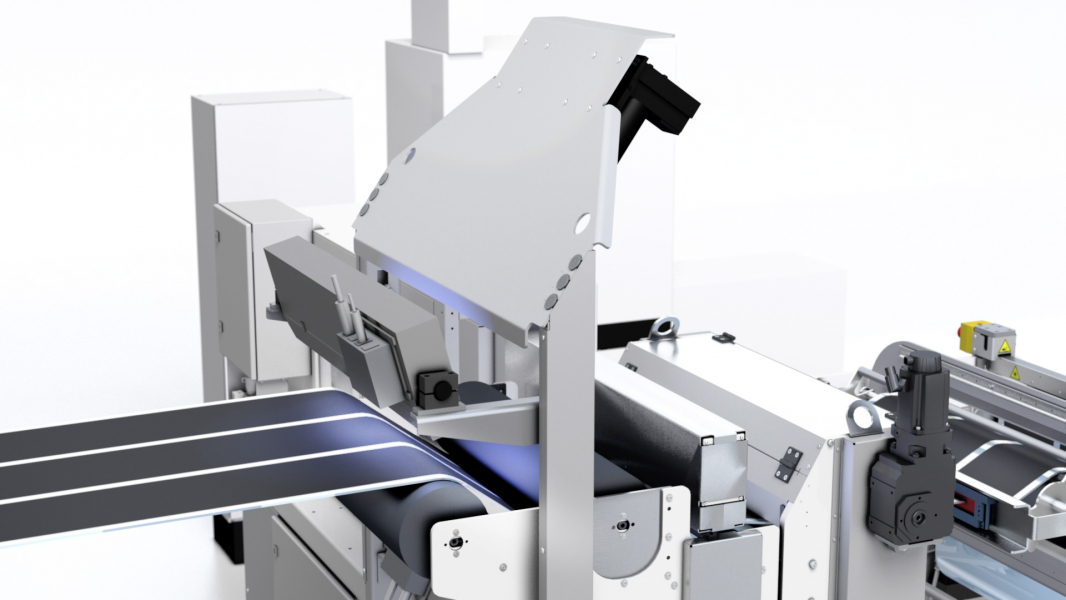
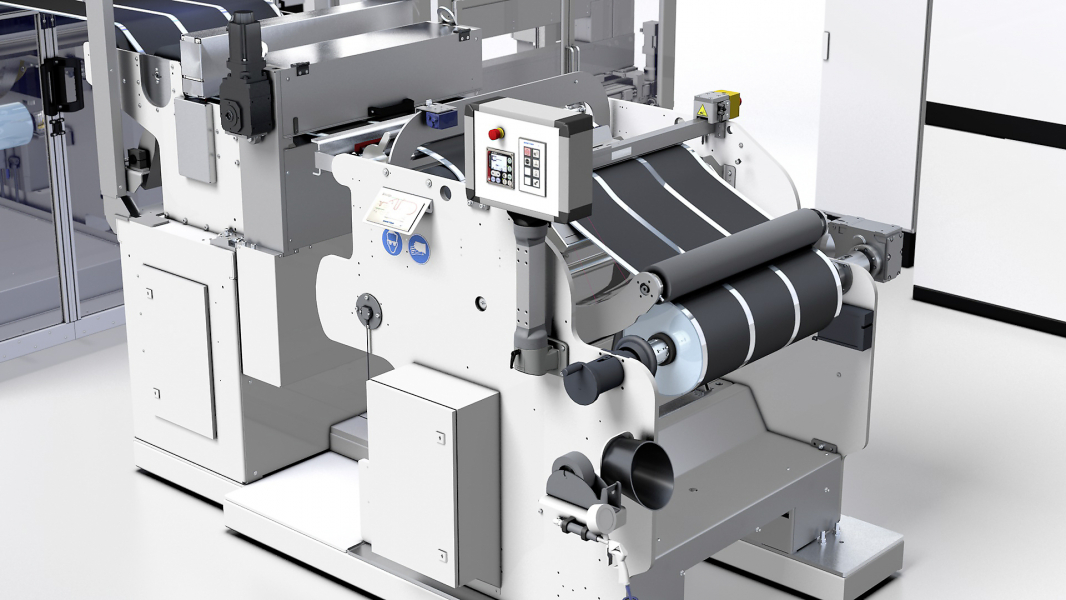
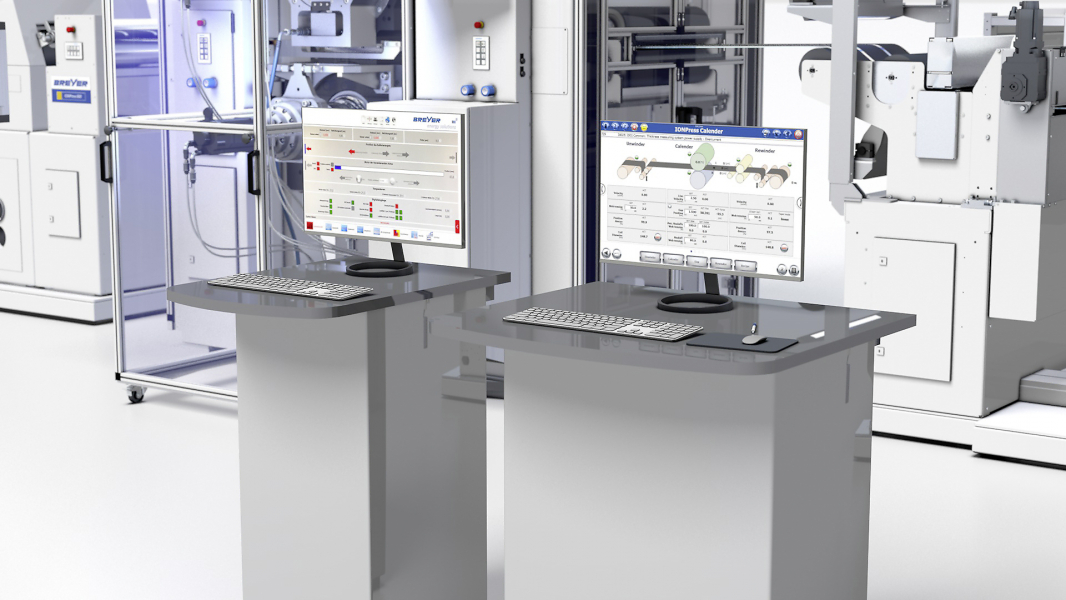